Efficiency at Its Best: The Lean Management Approach is an exploration of the Lean Management philosophy and principles, which have been developed over the past century as a way to improve productivity, quality, and customer satisfaction. The Lean Management approach is based on the Japanese concept of Kaizen, or continuous improvement, and seeks to eliminate waste and inefficiency in all areas of business. Historically, the Lean Management approach has been used in manufacturing and production, but has more recently been adapted for use in other industries and organizations, such as healthcare and government.
The philosophy and principles of Lean Management focus on the creation of value for the customer by eliminating non-value-added activities and reducing waste. This is achieved through a structured process of continuous improvement, which is focused on identifying and eliminating activities that are costly, but do not add value to the customer. Lean Management also emphasizes the importance of collaboration, communication and organizational learning, which helps to ensure that problems can be identified and solved more quickly and efficiently. Finally, Lean Management encourages the development of an organizational culture that values improvement and innovation, which helps to ensure that the organization remains competitive in the marketplace.
Benefits of Lean Management
1. Increased efficiency: Lean Management is a system of strategies and processes that focus on the elimination of waste in the production process. It is designed to maximize efficiency, reduce costs, and optimize the use of resources. Lean Management utilizes a variety of tools and techniques, such as value stream mapping, process optimization, and kaizen, to identify and eliminate non-value added activities from the production process. This results in increased efficiency, allowing businesses to produce more with fewer resources.

2. Improved quality: Lean Management is a system of strategies and processes that focus on improving the quality of products and services. It is designed to increase customer satisfaction by eliminating defects and improving product performance. Lean Management utilizes a variety of tools and techniques, such as total quality management, Six Sigma, and continuous improvement, to identify and reduce sources of variation and defects in the production process. This results in improved quality, allowing businesses to deliver high-quality products and services.
3. Reduced costs: Lean Management is a system of strategies and processes that focus on reducing costs and increasing profitability. It is designed to eliminate waste and streamline the production process, resulting in lower costs and improved efficiency. Lean Management utilizes a variety of tools and techniques, such as just-in-time production, process optimization, and total productive maintenance, to identify and reduce sources of waste and inefficiency in the production process. This results in reduced costs, allowing businesses to increase their profitability.
4. Enhanced customer satisfaction: Lean Management is a system of strategies and processes that focus on improving customer satisfaction. It is designed to increase customer loyalty by providing high-quality products and services that meet customer expectations. Lean Management utilizes a variety of tools and techniques, such as customer feedback systems, process optimization, and total quality management, to identify and reduce sources of customer dissatisfaction. This results in enhanced customer satisfaction, allowing businesses to build long-term relationships with their customers.
5. Increased employee engagement and morale: Lean Management is a system of strategies and processes that focus on improving employee engagement and morale. It is designed to create a culture of continuous improvement and provide employees with the tools and support they need to be successful. Lean Management utilizes a variety of tools and techniques, such as job rotation, process optimization, and kaizen, to identify and reduce sources of employee dissatisfaction. This results in increased employee engagement and morale, allowing businesses to create a productive and motivated workforce.
The Five Principles of Lean Management
Value: Value is the foundation of the Lean Management system. It is the process of identifying customer needs and delivering products or services that meet those needs. It is a customer-centric approach that focuses on delivering high quality products and services quickly and efficiently. Value stream mapping is an effective tool used to identify and eliminate waste in the production process and create more efficient processes.
Value Stream: Value stream mapping is a process used to identify and eliminate waste in the production process. It focuses on the flow of materials and information from the customer to the supplier, helping to identify where the most value is being created and where waste is occurring. It also helps to identify areas of improvement and opportunities to increase efficiency.
Flow: Flow is an important principle of Lean Management. It focuses on creating an uninterrupted flow of materials, information and activities within the production process. By focusing on the flow of materials and information, Lean Management helps to reduce waste, improve throughput and increase efficiency.
Pull: The pull system is a Lean Management principle that focuses on creating a demand-driven system. This means that the production process is only triggered when the customer needs a product or service. This helps to reduce waste, increase efficiency and reduce costs.
Perfection: Perfection is the ultimate goal of Lean Management. It is a continuous improvement philosophy that focuses on striving for perfection in all aspects of the production process. Perfection is achieved by identifying and eliminating waste, creating an efficient flow of materials and information, and creating a demand-driven system. By continuously improving the production process, Lean Management helps to create products and services that are of the highest quality and add value to customers.
Tools and Techniques used in Lean Management
Value Stream Mapping: Value Stream Mapping (VSM) is a Lean management tool used to identify, analyze and optimize all the processes involved in the flow of materials and information from supplier to customer. It helps in eliminating all non-value adding activities in the process and provides a clear picture of the current state of the process. It also helps in identifying potential problems and areas for improvement.
5S (Sort, Set in Order, Shine, Standardize, Sustain): 5S is a Lean tool used to organize, maintain and improve the workplace. It involves the following steps: Sort – Identifying items that are not required in the workplace and disposing them off; Set in Order – Arranging the workplace in an orderly manner; Shine – Cleaning and maintaining the workspace; Standardize – Developing standards and procedures to maintain the workplace; Sustain – Developing and implementing processes to ensure that the workplace remains organized.
Kaizen: Kaizen is a Japanese term meaning “continuous improvement”. It is a Lean tool used to constantly identify and eliminate waste, improve productivity and reduce costs. It involves a systematic approach to finding and eliminating waste in all aspects of the production process. It is based on the principles of teamwork, involvement and commitment from all levels of the organization.
Just-in-Time (JIT): Just-in-Time (JIT) is a Lean tool used to reduce lead-times, improve quality and reduce inventories. It involves the production of only what is needed and when it is needed. This helps in reducing the amount of inventory held by the organization and in turn reducing costs.
Kanban: Kanban is a Lean tool used to improve the flow of materials and information throughout a production system. It involves the use of visual signals such as cards or boards to alert employees when supplies are running low. This helps in reducing lead-times and improving the overall efficiency of the production process.
Poka-yoke (Error-proofing): Poka-yoke (Error-proofing) is a Lean tool used to reduce the number of mistakes made in the production process. It involves the use of various devices to ensure that only the correct parts and materials are used in the production process. This helps in reducing the amount of scrap and rework, which in turn reduces costs.
Andon: Andon is a Japanese term meaning “signal” or “flag”. It is a Lean tool used to indicate problems or abnormalities in the production process. It usually consists of an illuminated sign or light that alerts employees when there is a problem that needs to be addressed. This helps in quickly identifying and resolving issues and in turn improving the efficiency of the production process.
Total Productive Maintenance (TPM): Total Productive Maintenance (TPM) is a Lean tool used to ensure the availability of machines and equipment. It involves the use of preventive maintenance strategies to reduce the likelihood of equipment breakdowns. It also involves the use of predictive maintenance strategies to identify and correct any potential problems before they occur. This helps in reducing downtime and improving the overall efficiency of the production process.
Implementation of Lean Management
1. Identify and prioritize areas for improvement: The first step in implementing Lean management is to identify and prioritize areas that need improvement. This can be done by conducting an analysis of the current processes and identifying areas that are inefficient or could be improved upon.
2. Establish goals and objectives: Once the areas to be improved have been identified, the next step is to establish goals and objectives to help guide the implementation of Lean management. These should be based on the desired outcomes and the resources available.
3. Develop a plan of action: After goals and objectives have been established, the next step is to develop a plan of action that outlines the steps required to implement Lean management. This should include identifying the resources needed, creating timelines and assigning responsibilities.
4. Train staff: Once the plan of action is in place, it’s important to ensure that staff are properly trained to understand the Lean principles and how to apply them in their daily work. Training should include classroom instruction, on-the-job training and mentoring.
5. Monitor and measure progress: Once the training is complete, it’s important to monitor and measure the progress of the Lean implementation. This can be done by tracking metrics such as cycle times, cost reduction, process improvement and customer satisfaction.
Key Success Factors for Implementing Lean Management
1. Leadership commitment: The success of Lean management depends on the commitment of leadership to the process. Leadership must be willing to invest the necessary time and resources to ensure the successful implementation of Lean management.
2. Clear communication: Clear and effective communication between all stakeholders is essential for successful Lean management. This includes senior management, employees, suppliers and customers.
3. Continuous improvement: The success of Lean management relies on the ability to continuously identify and improve processes. This requires creating a culture of continuous improvement that encourages employees to identify and implement solutions.
4. Measurement and feedback: Measuring progress and providing feedback is essential for successful Lean implementation. This includes tracking key metrics, such as cycle times, cost reduction and process improvement, as well as providing feedback to employees on their performance.
Common Challenges Faced During Implementation and How to Overcome Them
1. Resistance to change: One of the most common challenges faced when implementing Lean management is resistance to change from employees. This can be overcome by communicating the benefits of Lean management and addressing any concerns that employees may have.
2. Lack of resources: Another common challenge is a lack of resources, such as time and money, to implement Lean management. This can be overcome by prioritizing areas for improvement and focusing on those that offer the most value.
3. Poor quality data: Poor quality data can make it difficult to accurately measure progress and identify areas for improvement. This can be overcome by ensuring that data is accurate, up-to-date and easily accessible.
4. Poor training: Poor training can lead to a lack of understanding of the Lean principles and lead to errors. This can be overcome by providing comprehensive training that covers all aspects of Lean management and ensuring that employees are properly trained and equipped to apply the principles in their daily work.
Case Studies on Lean Management
One of the most successful implementations of Lean Management is seen in the automotive industry. Toyota Motors, the Japanese automobile manufacturer, is known to have made significant use of Lean Management principles to reduce waste and waste management costs. Additionally, the company was able to reduce its overall production costs by eliminating unnecessary labor, redundant processes, and improving production flow. As a result, Toyota was able to produce more vehicles in a shorter period of time, and reduce its overall production costs.
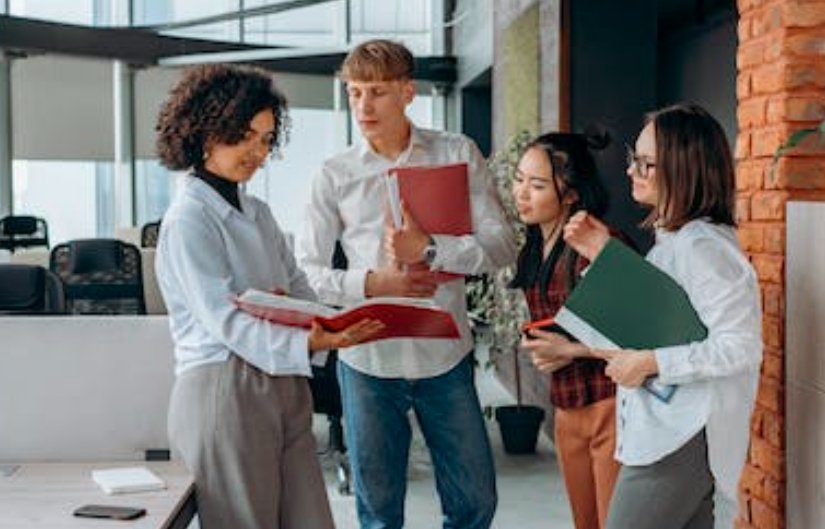
Another successful implementation of Lean Management was seen in the food and beverage industry. Coca-Cola, the world’s largest beverage manufacturer, was able to reduce its waste management costs by implementing Lean Management principles. The company was able to streamline its production processes and eliminate unnecessary steps, resulting in a significant reduction in waste and cost savings. Additionally, the company was able to improve its efficiency and reduce its production costs.
The healthcare industry has also seen successful implementations of Lean Management. The Mayo Clinic, one of the world’s leading healthcare providers, was able to reduce its waste management costs and improve its efficiency by implementing Lean Management principles. By streamlining its processes, the clinic was able to eliminate wasteful steps, reduce the time spent on administrative tasks, and improve the overall flow of its operations. As a result, the clinic was able to reduce its overall cost of care and improve its patient satisfaction.
The benefits of Lean Management have been seen across all industries, and have resulted in significant cost savings and improved efficiency. Companies that have implemented Lean Management have been able to reduce their waste management costs and improve their efficiency. Additionally, these companies have been able to reduce their overall production costs, and improve their production flow. Furthermore, Lean Management has enabled companies to improve their customer satisfaction and strengthen their market position.
Conclusion
The Lean Management Approach has revolutionized the way businesses operate, providing them with the tools and processes necessary to improve efficiency and reduce waste. This approach has been successfully implemented in a variety of industries, from manufacturing to healthcare, and is proving to be the leading approach to achieving maximum efficiency. As businesses continue to strive for excellence, the Lean Management Approach is providing them with the tools they need to succeed.
The Lean Management Approach has proven to be a powerful tool in helping businesses achieve greater efficiency. Its focus on continuous improvement, waste reduction, and value stream mapping has allowed organizations to streamline their processes, identify potential inefficiencies, and eliminate non-value added activities. Implementing the Lean Management Approach is an effective way to drive greater efficiency and productivity while maintaining quality and customer satisfaction.
The Lean Management Approach has been embraced by organizations around the world, demonstrating the value of this approach in helping businesses become more efficient. The success of this approach is attributed to its focus on continuous improvement and waste reduction, which are essential components of any successful business. By utilizing the Lean Management Approach, organizations can ensure that their operations are running at its most efficient and effective level.
In conclusion, the Lean Management Approach has revolutionized the way businesses operate, providing them with the necessary tools and processes to achieve greater efficiency. By utilizing this approach, businesses can eliminate waste, streamline processes, and identify opportunities for improvement. The Lean Management Approach is the leading approach to achieving maximum efficiency, and it is essential for businesses to embrace this approach if they want to remain competitive and successful.
FAQs
1. What is Lean Management?
Lean Management is an approach that focuses on maximizing customer value while minimizing waste. It is a systematic way of streamlining processes, eliminating non-value-added activities, and improving overall efficiency.
2. What are the key principles of Lean Management?
The key principles of Lean Management include eliminating waste, creating flow, and continuously improving. Lean Management can also be thought of as a set of tools and techniques used to identify and eliminate sources of waste, improve the efficiency of operations, and create value for customers.
3. How can Lean Management help improve efficiency?
Lean Management can help improve efficiency by reducing steps in processes, eliminating non-value-added activities, and improving the flow of information and resources. It also encourages employees to take initiative and identify areas for improvement.
4. What are the benefits of Lean Management?
The benefits of Lean Management include reduced costs, improved quality, and increased customer satisfaction. Additionally, Lean Management can result in improved employee morale and engagement, as well as increased flexibility and agility in responding to customer needs.
5. What is Kaizen?
Kaizen is a Japanese term meaning “change for the better”. It is a core element of Lean Management and focuses on continuous improvement. Kaizen encourages teams to identify potential areas of improvement, experiment with new solutions, and implement changes that will drive efficiency and effectiveness.
6. What is Value Stream Mapping?
Value Stream Mapping is a Lean Management technique used to identify and eliminate waste in a process. It involves mapping out each step in a process and analyzing it for areas of waste or non-value-added activities. This allows teams to identify opportunities for improvement and create more efficient processes.
7. What is the Theory of Constraints?
The Theory of Constraints is a Lean Management tool used to identify and eliminate bottlenecks in processes. It focuses on identifying the “constraint”, or the step in the process that is limiting the overall efficiency and throughput. By identifying and eliminating the constraint, teams can increase efficiency and reduce waste.
8. What is Six Sigma?
Six Sigma is a process improvement methodology used to reduce defects and variation in processes. It is based on a set of tools and techniques used to identify and eliminate sources of waste and variation, and improve the overall efficiency of operations.
9. What is 5S?
5S is a Lean Management tool used to organize the workspace and create a safe and efficient environment. It stands for Sort, Set in Order, Shine, Standardize, and Sustain. 5S is used to ensure that all necessary tools and equipment are easily accessible, and that the workspace is free of clutter and debris.
10. What is Kanban?
Kanban is a Lean Management tool used to visualize workflows and limit the amount of work in progress. It is based on a set of cards used to represent tasks, and is used to monitor and track the progress of projects. Kanban can help teams identify potential areas of improvement and bottlenecks in processes.